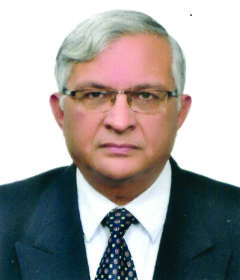
Wg Cdr Rakesh Kumar Prashar
Safety Professional
Safety Professional
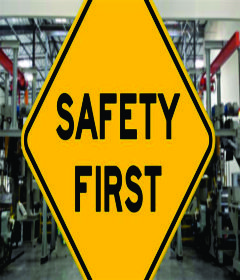
Wg Cdr Rakesh Kumar Prashar
Q: With economic growth OSH has become a very important subject. How do you see safety implementation in India?
In spite of the multifarious issues that plague India, it is a matter of happiness that record growth rates have been recorded in almost all the sectors in the last two decades or so. The matter of cheer for us safety professionals is that as far as OSH awareness is concerned, at least we are on the right path even though the growth is not as much as was expected.
As far as the safety implementation in India is concerned, I feel, two words define the reality of safety in India – ‘’Chalta Hai” and ‘Jugaad’. The reason for this state of affairs in my opinion is lack of three essential ingredients essential for success in safety – legal will, management commitment and employee engagement.
- Lack of legal will to enforce safety: It is a well known fact that the figures reported to the enforcement agencies are much lower than the actual figures. The management as well as the enforcement agencies are both to be blamed for this situation. To add to this embarrassment, it is learnt that there is only one inspector for every 506 registered factories in India. With such poor infrastructure and lack of will, ensuring 100% safety compliance is a tough challenge.
- Lack of management commitment to safety: Some organisations give safety a very low priority because they value the management of capital or technology more than the management of people. The focus on ‘Production’ results in the workers also giving safety less priority than it deserves, leading to basic safety violations and injuries / fatalities as a consequence thereof. With genuine management focus on safety, the continuing spate of accidents in India could have been averted.
- Lack of employee engagement in the safety effort: Without employees’ engagement and continued involvement, even the best processes, programs and procedures are worthless. The employees resort to short cuts and wrong doings just to save a minute or two with a view to impressing the management, while the supervisors overlook the workers wrongdoings with a view to focus on production to impress the management.
While ‘Legal will’ sets the framework for safety, ‘management commitment’ sets the foundation for a safe workplace and ‘employees’ engagement’ in safety activities, helps build a strong edifice. If management commitment, employee participation and legal will are displayed effectively, the safety situation in India will see a sea change.
Q: How far have we to go to match international safety standards in our industries?
While we still have a lot of catching up to do to match the international standards, what is heartening is the fact that the gap is reducing, albeit slowly. Stricter labour laws alone will not suffice. Its success lies in strict implementation for this alone can contribute to higher efficiency, increased productivity and faster growth. The plan to merge 13 major laws into a single labour code on Occupational Safety, Health and Working Conditions by the Ministry of Labour & Employment which is in the final stages will go a long way in this direction.
Nevertheless, benchmarks have been set and major industries are voluntarily following OHS norms as are the MNC’s and Indian corporates. I am very hopeful that the next decade will be a defining period for Indian industry and we will be fortunate to see a different India as far as safety is concerned.
Q: What area of scope still is needed by Indian industry while implementing safety norms?
We don’t think twice before doing something wrong or taking shortcuts simply because we feel that the chances of getting hurt are too low to prevent us from taking the risk. This behaviour needs to change. A paradigm shift from ‘Safety is a priority’ to ‘Safety is a value’ is required to improve the safety scenario in India for which we have to move from ‘Chalta Hai’ to ‘Nahi Chalega’. Towards this aim, I personally feel that two words should be removed from our dictionary if we want to succeed in our safety endeavour – ‘Sorry’ and ‘Compromise’. If we can do so, our success is assured. STILL
We will be doing a big disservice to ourselves if we blindly copy safety norms followed by international organisations. To succeed we must understand the ethos behind the same and ensure that itis followed both in letter and spirit. I am aware of companies where the system of the first slide to be on safety in a meeting was diligently followed but after that safety was not part of the discussions anymore.
Action like annual appraisal linked to the HSE performance, variable pay release linked to the accident rate, defined safety budget for the projects / industry, HSE department being empowered in line with the production department, recognition and reward for outstanding employees for their contribution to safety rather than reward high production targets, train employees routinely etc are steps where we need to focus on improving our safety performance.
Q: What scope of safety industry of India do you see in coming 10 years from now?
India's infrastructure growth be it water supply, sewerage, communication, roads, highways & bridges, airports, shipping, railways, housing, urban services, mining, energy, oil & gas or power has been exponential over the past decade or two. Today, we are the fourth largest and probably the second fastest growing economy in the world. While the governments dream of making India a $5 trillion economy by 2024 may seem exaggerated for the moment, but the international companies will definitely sense the opportunity and look for a slice of the cake in the high growing Indian market.
The coming 10 years will definitely see India’s private sector lead this transformation on account of their ability to adapt to new business models and new technologies. This will expose them to new practices and innovative products being produced by the global companies with a view to adopt the same in India too. Over a period of time, the Indian companies will invest more in R&D so as to develop capabilities and challenge the global companies with a view to serve both - India’s growing domestic market as well as to compete on the global stage.
With so much at stake and the rising value for life in India due to the global companies’ presence, can the safety industry in India be left behind? With ISO 45001 becoming more stringent and IFC’s enforcing strict compliance of its EHS norms for availing loans for big projects, the scope of safety industry in India in the next decade or more is extremely bright. Although the competition is tough, the winners will be the ones who are focused, innovative, creative and regularly upgrading their products.
Q: What more role of government do you see to uplift safety standards in India?
The rapid growth recorded by the Indian Industry over the last two decades which has resulted in increased manufacturing activities, technological advancements and infrastructural development is likely to further accelerate in the next decade or so. This rapidly changing environment calls for not only improved standards, but also strict application of laws pertaining to health & safety of workers. This will not only improve the health & safety of the working population but also ensure increased productivity.
Some steps the government can take to uplift the standards of safety in India include:
- The umpteen laws pertaining to health and safety of workers in India must be merged into a single comprehensive law which can easily be understood by the management as well as the workers and an apex institution created to ensure its strict implementation across all the sectors. Work on the same is already on the government’s agenda. A draft bill to merge 13 major laws into a single labour code on Occupational Safety, Health and Working Conditions has already been prepared by the Ministry of Labour & Employment. The earlier this labour reform is finalised, the better it will be as it will not only contribute to increased health & safety of the workforce, but also improved efficiency, increased productivity and greater growth. As part of this reform, the top management alone must be made accountable for any injury / fatality in the projects and industries. This will automatically increase the safety in the organisations as well as in the country as a whole.
- Ensuring effective and genuine half yearly safety audits of all factories and industries by statutory Health and Safety bodies in the states. To ensure this, workload management of the Inspectorates of Factories / Directorates of Industrial Safety and Health in the states must be optimized so as to ensure that there is one inspector for not more than 20 - 25 registered factories in India. This will also check the massive under-reporting of the safety figures which is a well known fact.
- More safety training institutes must be created to produce high caliber safety professionals and their employability must also be ensured. The safety officers thus produced and placed, must also be given more teeth so as to ensure that safety is genuinely catered to and not dictated by the whims and fancies of the corporates. These institutes can also conduct skill development courses especially of the migrant labourers in the safety field. This will help in achievement of the long term aim of improving the safety culture not only of the corporates but also of our nation.
- Lastly, the will to act has to be demonstrated by the government in the safety domain by imposing heavy penalties on companies for any safety violations and non-reporting / under-reporting of incidents on the lines of the recent amendments of the Motor Vehicles Act to improve road safety. This will not only act as a deterrent, but also impose self discipline.
These action by the government will greatly help in creating a positive safety culture in India.
Q: What is the area of scope for safety manufacturers in India?
The rapid infrastructural growth in India coupled with the increasing value for life and stringent fire and safety regulations is likely to influence the fire and safety equipment market in India in a very big way in the next decade or so. This market is forecast to grow at a CAGR of more than 8% due to which various MNCs in the safety domain too are making a beeline for Indian shores. At such times, it is important that the Indian fire and safety manufacturers not only adapt to new business models and technologies but also increase investments in R&D so as to develop creative solutions keeping in mind the Indian scenario and mindset. This will not only help them to serve India’s growing domestic market, but also enable them to compete on the global stage. The make in India initiative will also help them in this endeavour.
Q: We have witnessed many accidents in small scale industries due to lack of proper safety norms implementation. How attitude for safety can be imparted in them?
The spate of accidents not only in the small, but even the medium and large scale industries due to lack of proper safety implementation is a cause for very serious concern. The root cause for this is what I call a negative safety culture in the organisations. Why I call it negative safety culture is because the word ‘Safety’ in itself generates negative feelings and draws a sneer even in the highest echelons of management, not to talk of the workers levels. Expenditures incurred on safety are considered as a ‘Cost’ rather than an ‘Investment’ and safety personnel are seen more as a ‘Pain in the neck’ rather than a ‘Friend, philosopher & guide who help the company grow’ that they actually are.
I believe that the day management realises that ‘safety does not cost, it pays’ and the workers realise that ‘safety is not a pain, it is a gain’, the journey to development of a positive safety culture will commence. The key to developing a positive safety culture in the organisation does not lie in reducing the number of accidents and subsequent fatalities or injuries, but in recognising that accidents can be prevented if the correct procedures and systems are followed in letter and spirit and taking action to ensure the same. Now the question, how can this be done? All of this requires a two pronged action:
- Developing safety leaders. One key element of developing effective safety leadership is inspiring a shared safety vision. If the leaders have a vision, even the impossible will become possible. If the leaders themselves do not have a safety vision and/or do not possess the ability to communicate the same in a simple, clear, bold, and convincing manner to their employees, then the employees too are neither inspired nor committed to a shared goal. While safety rules, procedures and systems do exist on paper, they remain so, because productivity becomes the primary focus at all levels. The leaders must focus on productivity but not at the cost of safety. It must be realised that the day the focus shifts from productivity to safety, productivity will automatically increase bringing in a windfall. The reverse is never possible.
- Imparting training at all levels. People who are properly trained in their jobs and are aware of the hazards associated with the role they perform or supervise, are less likely to suffer or cause injury. Learning helps us to become better professionals. It is not just technology or processes related training that one must constantly undergo and upgrade, but also behavioural safety skills. The functional purpose of Behaviour Based Safety (BBS) training is to improve the performance of the trainees by impacting their behaviour. If BBS training is focused from the outset, it will help the employees reduce the number and frequency of their identified at-risk behaviors. When the individuals at all levels display a positive attitude to safety in all their action or inaction, a sound safety culture is the outcome which brings in everlasting peace and happiness to all the individuals as well as the organisation. However, to succeed, training should be an ongoing process and must encompass all personnel from the top to the grass root level workers.
These steps will not only drastically reduce accidents in India, but also ensure that the changed attitude will help sustain the benefits continually. An ILO study revealed that countries with a lower number of accidents achieve a higher level of competitiveness. Thus a proactive occupational health and safety management system will not only help increase the employee commitment and improve the safety culture of the organisation, but also enhance its image, reputation and competitiveness globally.
Q: Any message for the readers?
The alarming increase in accidents across all sectors in India has proved that there is much more than just meeting statutory requirements and that safety has become an absolute necessity not only in economic, but also social & ethical terms. An ILO study has reported that the cost of accidents globally amounts to around 4% of the global GDP which translates into trillions of dollars loss annually. Since India accounts for a massive percentage of the accidents worldwide, the losses in the Indian context can be imagined.
This calls for a change of mindset from ‘Loss Prevention’ to ‘Life Preservation’ since this alone will lead to increased productivity and improved profitability for organisations. For this, participation of all in all the activities related to safety willingly and voluntarily is the need of the hour. Innovation and creativity in our safety related activities will also get us closer to our goals faster than we can imagine. While doing so, we must ensure that we do not depend on ‘Luck’ for success in safety, but on our ‘Actions’ to help us succeed in our safety efforts. Attitudinal change towards safety therefore is called for so as to help both - corporate as well as our national growth.
Wg Cdr Rakesh Kumar Prashar is a motivational speaker and Safety & Soft Skills trainer with over two decades experience in the Indian Air Force in the commissioned ranks and nearly two decades experience in the corporate world in the safety domain. He has conducted over a thousand safety training programmes in India and 30 countries worldwide and over 300 soft skills training programmes for corporates, schools, colleges & NGOs in India. He is empanelled with many corporates as a safety & soft skills trainer. He has received many awards and accolades including ‘Safety Professional Excellence Award’ at the World Environment Summit 2020 for excellence in safety training and ‘Best Trainer Award’ by Indian Society for Training & Development in 2013. He is empanelled with All India Radio as a sports commentator in English and a internet radio channel in English & Hindi. He has the unique honour of doing ‘Live’ commentary for both hockey and cricket World Cups. He has also done commentary for Junior World Cup, Champions Trophy, National Men’s & Women’s Championship in hockey as well as ODI matches and IPL in cricket World Cup 2019.
Recent Posts
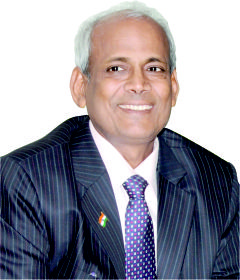
Padma Shri Jai Prakash Agarwal
Robust Growth: Surya Roshni Registers Over INR 8,000 Crore Sales in FY 2023-24
Surya Roshni, an Indian conglomerate, is among the oldest and largest pipe manufacturers in the country having a diverse product range, t...
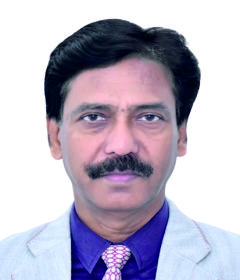
Mr. Dilshad Ahemad
Q. Can you tell me about your company & its history?
Yes sure, it reminds me of a young ambitious Management graduate from Bihar who comes to Delhi in search of Job as job opportunities in Bihar were bleak. I was lucky to hav...
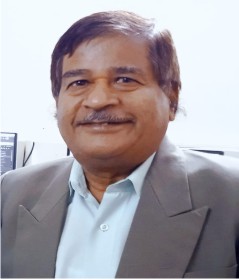
Mr. Pradeep Mandre
Q: Kindly let us know about M/s Divya Enterprises
M/s Divya Enterprises is a partnership company formed in year 2004 by enthusiastic engineers. We were in field execution for the initial span of 10 years dealing with project work...
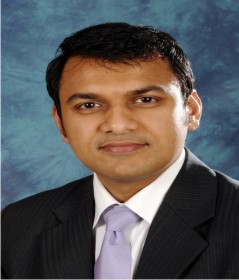
Mr. Praveen Khemka
Q: Can you please help us with your educational and professional background which would help our viewers connect with you better?
Praveen Khemka is a B Tech Civil, IIT KGP graduate and MBA in Strategy & Finance, WHU Vallendar...
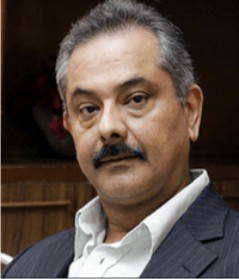
Mr. Rajan Sharma
Q: Can you tell us about Milipol India?
A: Milipol India is the Leading International Event for Homeland and Internal Security for Indo-Pacific, which will be held in New Delhi from the 26th to 28th October 2023....