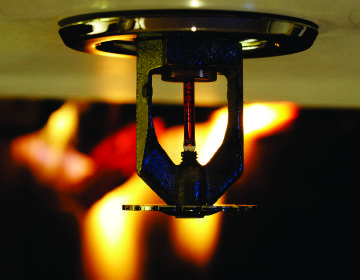
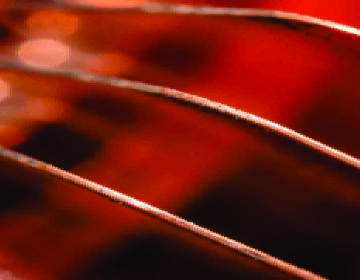
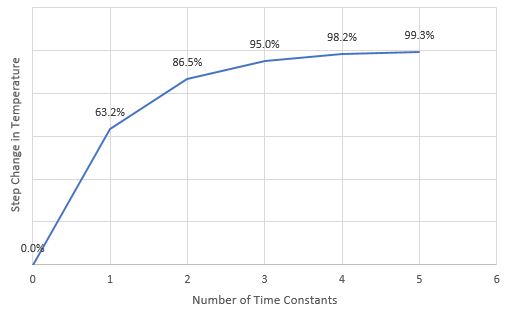
Characterization of the sprinkler water spray through CFD Modelling
Characterization of the sprinkler water spray through CFD Modelling
Aravind Kumar. A*, Rajiv Kumar and R. S. Chimote
Fire Research Division,CSIR-Central Building Research Institute, Roorkee, Uttarakhand, India-247667.
ABSTRACT
The present study investigates water sprinkler characteristics for fire suppression system using Computational Fluid Dynamics (CFD). CFD simulations are carried out to investigate the interactions between sprinkler water spray and heated zone fire fields. The domain size taken for the study is 0.3 m*0.3 m*0.6 m. The heated zone size for the model 0.1 m*0.1 m. Buoyancy turbulence is taken into consideration for the heat transfer in the domain. Droplet tracking method Eulerian–Lagrangian used for the investigation of fire and sprinkler interaction. The simulation of water sprinkler and fire behaviour is employed by using a commercial code CFX-5. Fire suppression efficiency based on different water spray characteristics such as droplet size, injection angle and water mass flow rates is investigated.
Keywords: Multi-Phase modelling, Fire suppression, Droplet diameter, Sprinkler, Spray angle, Lagarangian method, Particle.
1. INTRODUCTION
Water has been used for controlling fires since the ancient time. That is because water is readily available and inexpensive in most areas. It is nontoxic, and can absorb large amount of heat due to its latent heat of vaporization and high specific heat capacities in both liquid and gas phases. There are two methods of applying water for fire fighting, i.e. jet branch and spray branch. Bulk liquid is applied in the jet branch to cool down the flame and the burning surface using hose reel or fire hydrant systems. Other means such as pouring a basin of water into the fires can also be classified under this method. Large amount of water would be wasted and lead to severe water damages, though jet branch can prevent the combustible surface to the ignition. In practice, automatic sprinkler system and fixed water spray system are used as fire services installations. Fire suppression with water sprays is reviewed by Grant et al. [1].
Water mist fire suppression systems are now commonly used as an alternative to the halon total flooding system. However, water mist does not behave like a real gas and not all of them are involved directly in fire suppression. There are a number of studies have been developed for water mist fire suppression system over the past ten years. Water mist has been used as total flooding agent for some large scale compartment by K.C.Adiga [2]. Almost a similar work is then done by Y.Sinai et al. for pool fire in a room by using ANSYS CFX [3]. Some experimental work has also have been done and then CFD modelling is being done for the validation and comparison as well. A similar work is done by Thomas K.Blanchat, and by Sam S. Yoon, for a 2 meter fuel pan [4].
Computational fluid dynamics (CFD) studies in the past have focused on the interaction of water mist with fires is reported by R. Mawhiney [5] and K.Prasad [6]. The emphasis of the present study is on designing total flooding fire test parameters to evaluate the performance of a proprietary UFM provided by NanoMist Systems, LLC. FLUENT [7], a commercial CFD program was used with relatively simple sub-model elements. Since the objective was to model UFM transport and entrainment of mist into the firebase, a simple pool-like hot gas fire was used by K.C.Adiga[8,9]. Combustion chemistry and radiation sub-models were not activated in this study. As the computationally cost-effective approach, the Discrete Phase Model (DPM) of CFD was used to simulate the mist transport and entrainment of mist into the firebase and the cooling of the fire by droplet vaporization. Additional simulations were carried out treating UFM as a dense gas using the species transport model. The paper is not reporting any experimental data validation but it will give an approach for the multi-phase modelling and simulation through CFD.
2.0 MULTI-PHASE MODELLING.
Multiphase flow refers to the situation where more than one fluid is present. Each fluid may possess its own flow field or all fluids may share a common flow field. Unlike multicomponent flow, the fluids are not mixed on a microscopic scale in multiphase flow. Rather, they are mixed on a macroscopic scale, with a discernible interface between the fluids. CFX includes a variety of multiphase models to allow the simulation of multiple fluid streams, bubbles, droplets, solid particles, and free surface flows. Two distinct multiphase flow models are available in CFX, an Eulerian-Eulerian multiphase model and a Lagrangian Particle Tracking multiphase model. Eulerian-Lagrangian Particle Tracking model is chosen for the study.
Particle transport modelling is a type of multiphase model, where particulates are tracked through the flow in a Lagrangian way, rather than being modelled as an extra Eulerian phase. The full particulate phase is modelled by just a sample of individual particles. The tracking is carried out by forming a set of ordinary differential equations in time for each particle, consisting of equations for position, velocity, temperature, and masses of species.
The continuous gas flow is air (as ideal gas) and the water as particle transport fluid which is solved using ANSYS-CFX unsteady solver. The spray is considered as axisymmetric around the z axis running out from the initial position. The drop size distribution is considered as uniform and also spray is released in an infinite gas phase initially at hot boundary conditions of near steady state.
2.1 Heat transfer modelling
The Modelling of heat transfer in the domain uses the basic continuity, momentum, thermal energy with the -
Model being used. The transient analysis study is chosen to account the fire dynamic behaviour. The governing equations for the simulations are available literature.
2.2 Eulerian-Lagrangian modelling
The Eulerian-Lagrangian method for simulating two-phase flow has been investigated in detail. The gas phase is regarded as a continuum while the liquid droplet phase is treated as individual particles traced by the Lagrangian approach. Key elements of this technique in modelling of water sprays will be discussed in this section.
The equation of a single spherical droplet motion in turbulent flow field forms the base of Lagrangian modeling for sprays. In a general form, this equation is reported by K.K.Kuo [10]:
The terms on the right-hand side represent, drag force, force due to static pressure gradient, virtual-mass term, basset force to account for effects of deviation of the flow from a steady flow pattern around the sphere and external body-force, e.g. gravity. Detailed considerations of the relative importance of each term are provided by Faeth [11].
Turbulent dispersion of the droplets can be modelled by the stochastic discrete particle approach. In addition, this approach can be combined to model a set of clouds about a mean trajectory that includes the effects of turbulence fluctuations in the gas phase velocities [12].
The heat transfer equation must be considered for droplet in order to describe the history of droplet temperature and evaporation rate in fire environment. Assuming uniform temperature inside the droplets, this equation reported by S. Kumar[13]. The Ranz-Marshall correlations are commonly used to calculate the Nusselt and Sherwood numbers, which govern the heat and mass transfer processes. These are given as functions of Reynolds, Prandtl and Schmidt numbers [14,15].
3.0 GEOMETRY AND BOUNDARY CONDITIONS
CFD simulations are performed using ANSYS CFX-5. The foot print of the geometry is 0.3 m * 0.3 m cross section with a height of 0.6 m is chosen. The heated zone is of 0.1 m * 0.1 m is created at a height of 0.1 m from the ground. The heated zone is axis symmetrical from the centreline. ANSYS workbench Design Modeler is used to create the 3D geometry of the domain as shown in Figure 1.
The meshes were created using the mesh generator provided as part of the ANSYS CFX-5 module package. The details of the meshing used for the study are reported in the Table 1. The virtual mesh cell is like cone spray from the top to just above the fire source. This will enhance the improvement in the convergence temperature and velocity profiles of the water spray and fire interaction. Figure 2 gives view of the mesh domain. The fine mesh has a maximum face size of 0.001 m. These fining of mesh is done in order to get more accurate result in the nodes.
The simulation scheme is done in two configurations, one for heated zone and another with water spray activation. The heated zone simulation used is transient, for 3000 s with a step size of 1 s. The water spray simulation is done for 2 s with a time step size of 0.001 s. The default domain is defined as fluid domain with particle transport phase. Air (as ideal gas) is continuous fluid with Water as particle transport fluid. The domain reference pressure is considered as 1 atm. The buoyancy turbulence is considered with an air density of 1.2 kg/m3. The Thermal energy heat transfer is chosen to study the convection and conduction phenomena. The radiation effect is not taken in to account. The -
model is chosen to represent the fire turbulence in the domain. The heat transfer model chosen for the water is particle temperature between the air and water interaction. Ranz marshall correlations used for the heat transfer between air and water interaction with a surface tension coefficient of 0.07 Nm-1. The liquid evaporation is taken between the water and its vapour.
The walls of the domain are defined as no slip wall and adiabatic. Wall roughness is not taken in to consideration. Temperature in the heated zone is defined as 600 K with an area of 0.1 m * 0.1 m. The room domain is initialized at 300 K. The simulations were performed for the stabilization of the temperature inside the room for 3000 s to reach near the steady state.
The water sprinkler spray is initiated after 3000 s of the heated zone configuration. The initial conditions for the water sprinkler spray configurations are defined by the heated zone configuration. The water sprinkler spray is defined as particle injection and simulated for 2 s. Particle injection is from point cone at 0.59 m height from ground with an injection velocity of 60 m/s. Particle number rate is specified as 10000 s-1. The other characteristic parameters such as droplet diameter, mass flow rate and spray angle are chosen for the sensitivity analysis. Table 2 lists the values chosen for the study of fire suppression.
Table 2: List of parameters and values for sensitivity analysis
Run No |
Diameter in mm |
Mass flow rate in kg/s |
Spray angle in deg |
1 |
0.9 |
0.1 |
30 |
2 |
0.09 |
0.1 |
30 |
3 |
0.9 |
0.05 |
30 |
4 |
0.09 |
0.05 |
30 |
5 |
0.9 |
0.1 |
15 |
6 |
0.09 |
0.1 |
15 |
7 |
0.9 |
0.05 |
15 |
8 |
0.09 |
0.05 |
15 |
The differencing scheme utilizes High Resolution with second Order Backward Euler scheme for all the equations. Turbulence equations are solved in first order. The runs were performed on a windows server with Intel(R) Xenon(R) CPU with 12 GB ram. The runs took about 48 hours on an average for each simulation simultaneously.
4.0 RESULTS AND DISCUSSION
The detailed sensitivity analysis of the simulation is an extension study of S. M. Sumon and Sang-Wook Lee [19]. Simulation of fire and water spray sprinkler suppression is carried out in two configurations, without fire and subsequently with fire as described in previous discussion. The heated zone results of fire simulation velocities are observed after 200 s from the start of simulation time. The legend view indicates that the maximum velocity observed to be 0.1479 m/s and minimum velocity is 0.0045 m/s. The velocity vectors are measure at 3000 s and minimum and maximum velocities are as follows 0.1038 and 3.616 m/s. The pictorial representation of the simulations on a plane is as shown Figure 3. The velocity profiles of the heated domain gives an inference of minimum velocity of droplets needed for suppression.
The spray angle along with velocities of the particles in the sprinkler water spray domain above the heated zone is reported. The velocity of the particle at the centre line is very high and it decreasing when it approaches to wards the wall. The droplet velocities of the 15 deg and 30 deg are shown in Figure 4. The particles that are visible in the figures apart from the spray angle profile are the particle evaporated and moving in upward direction.
Transient analysis of temperature curve of the heated zone simulation is shown in figure 4. Measurement of the temperature reported is 0.1 m above fire source at centre point of the domain. The results of the trasient anlysis heated zone simulation is the intitial conditions for sprinkler domain for all senstivity studies.The slight bend in the curve near 1500 s is due to turbulence near the point of measurement. The temperature inside the domain is almost constant after 3000 s due to symmetrical boundary conditions.
Water spray sprinkler simulation studies reveal the performance and suppression efficiency of the fire. The suppression efficiency of the fire is tested for a total 8 runs (as per data of Table 2) of simulation for 2 s. The Time vs Temperature curve for suppression is presented in Figure 5 and 6 with the diameters of 0.9mm and 0.09mm.
The suppression time is taken for the study is taken as 2 s for both the particles. This is the reason we are presenting the results of temperature up to 2 s only. Results of figure 5 indicates, with a mass flow of 0.1 kg and a spray angle of 15 deg suppression efficiency is time is less compared to other runs of 0.9 mm dia particles. For the mass flow rate of 0.1 kg in both the runs the suppression time is less.
The fire suppression time is very less compared to 0.9mm particle dia with 0.09mm particle. From the figure 6, it clearly indicates that high mass flow rate of 0.1 kg with 30 deg cone angle takes less time for suppression, whereas 0.05 kg with 15 deg has taken more time for it.
It is evident from the figures, the higher the droplet size takes much time for suppression compared to lesser droplet size. This gives a conclusion that fire suppression can be achieved in less time, with high mass flow rate and optimum suppression spray angle. The statement of the above will be valid for the cases where the water sprinkler spray system installed in the wetted area of the sprinkler domain.
5.0 CONCLUSIONS
The water spray modelling for fire suppression is reported using Lagrangian particle tracking method with different characteristic parameter study. The future study will be reported on well validated full scale experimental data with discrete diameter distribution. Combustion modelling studies involvement in the fire suppression through CFD is a research gap still it has to be addressed.
6.0 NOMENCLATURE
CB Basset force coefficient
CD Drag coefficient
CI Virtual mass drag coefficient
dp Droplet diameter
Fe External body force
t Time
U Velocity vector
X Cartesian coordinate
Greek symbols
ρ Density
μ Dynamic viscosity
ξ Mixture fraction
Subscripts
P Particle
7.0 REFERENCES
- G. Grant, J. Breton and D. Drysdale, “Fire suppression by water sprays”, Progress in Energy and Combustion Science, Vol. 26(2), pp 79-130, 2000.
- K.C. Adiga, Robert F. Hatcher Jr, Ronald S. Sheinson, Frederick W. Williams and Scott Ayers, “A computational and experimental study of ultra-fine water mist as a total flooding agent”, Fire Safety Journal, Vol. 42(2),pp 150–160, 2007.
- Yehuda Sinai, Phil Stopford, Mike Edwards and Steve Watkins, “CFD modelling of fire suppression by water spray: sensitivity and validation for a pool fire in a room”, Eighth International IBPSA Conference Eindhoven, Netherlands August 11-14, 2003.
- Thomas K. Blanchat, Alexander L. Brown and Victor Figueroa, “Benchmark enclosure fire suppression experiments and modeling”, Suppression and Detection Research and Applications – A Technical Working Conference (SUPDET 2008), International Plaza Resort and Spa, Orlando, FL, March 11-13, 2008.
- Mawhinney R, Grandison A, Galea ER, Patel M and Ewer J, “The development of a CFD based simulator for water mist suppression systems: the development of the fire sub model”, Appl Fire Sci, Vol. 9(3),pp 11–46, 2000.
- Prasad K, Li C and Kailasanath K, “Optimizing water-mist injection characteristics for suppression of methane-air diffusion flames”, Twenty-seventh symposium (international) on combustion, the Combustion Institute, pp. 2847–55, 1998.
- Fluent user’s guide vols. 1–4. Fluent Incorporated, Central Resource Park, 10 Cavendish Court, Lebanon, NH 03766, 1998–2004.
- Adiga KC, Ramaker DE, Tatem PA and Williams FW, “Modelling pool like gas flames of propane”. Fire Saf J, Vol. 14, pp 241–50, 1989.
- Adiga KC, Ramaker DE, Tatem PA and Williams FW. “Numerical predictions for a simulated methane fire”. Fire Saf J, Vol. 16, pp 443–58, 1990.
- K.K. Kuo, “Principles of combustion”, New York: Wiley, 1986.
- G.M. Faeth, “Evaporation and combustion of sprays”, Progress in Energy and Combustion Science, Vol. 9, pp. 1-76, 1983.
- A.D. Gosman and E. Ioannides, “Modelling turbulent dispersion of the droplets by a stochastic discrete particle approach”, American Institute of Aeronautics and Astronautics (AIAA), Paper No. 81-0323, 1981.
- S. Kumar, G.M. Heywood and S.K. Liew, “Super drop modelling of a sprinkler spray in a two-phase CFD-particle tracking model”, Proceedings of the Fifth International Symposium on Fire Safety Science, pp. 889-900, 1997.
- W.E. Ranz and W.R. Marshall Jr., “Evaporation from drops: Part I”, Chemical Engineering Progress, Vol. 48(3), pp 141-146, 1952.
- W.E. Ranz and W.R. Marshall Jr., “Evaporation from drops: Part II”, Chemical Engineering Progress, Vol. 48(4), pp 173-180, 1952.
- V. Novozhilov, “Computational fluid dynamics modelling of compartment fires”, Progress in Energy and Combustion Science, Vol. 27(6), pp 611-666, 2001.
- D.J. Rasbash, “The extinction of fire with plain water: a review”, Proceedings of the First International Symposium on Fire Safety Science, pp 1145-1163, 1986.
- C.T. Crowe, “Two phase momentum, heat and mass transfer in chemical, process and energy engineering systems”, Washington: Hemisphere, Vol. 1, pp 23-32, 1978.
- S.M. Sumon and Sang-Wook Lee2, “A Numerical study of the Effects of Water Mist Characteristics”, Proceedings of the 13th Asian Congress of Fluid Mechanics, , Dhaka, Bangladesh, 17-21 December 2010.
Recent Articles
Ensuring Fire Safety: The Importance of Testing &a...
Ensuring Fire Safety: The Importance of Testing & Certificationas per Indian Standards
Author: Sandy Dweik, CEO of Thomas Bell-Wright
Fire safet...
The Significance of Print Media in Promotion in Re...
The Significance of Print Media in Promotion in Recent Times
Presented by: Mayur Lalit, Director, D V Enterprises
In an era dominated by digital technologies and online marketing, print me...
Safe Haven - Fire Safety at Home
Safe Haven - Fire Safety at Home
By: Rakesh Parashar, Safety Consultant
Fire is one of humanity's oldest and most significant discoveries, shaping the course of human ...
Fire Doors – LPCB helps to protect people and pr...
Fire Doors – LPCB helps to protect people and property
By: Kamil Hamid FIFSM (UK) ., Overseas Manager – BRE Group (LPCB)
The purpose of a fire door is to prevent th...
The Significance of Fire Suits and Their Future Pr...
Contributed by: Mr. Rahul Sakhuja
Director, Safety Experts
The Significance of Fire Suits and Their Future Prospects
Introduction
Fire suits, or firefighter turnout gear, ar...